Partnership for plant optimization - manure in, profitability rises
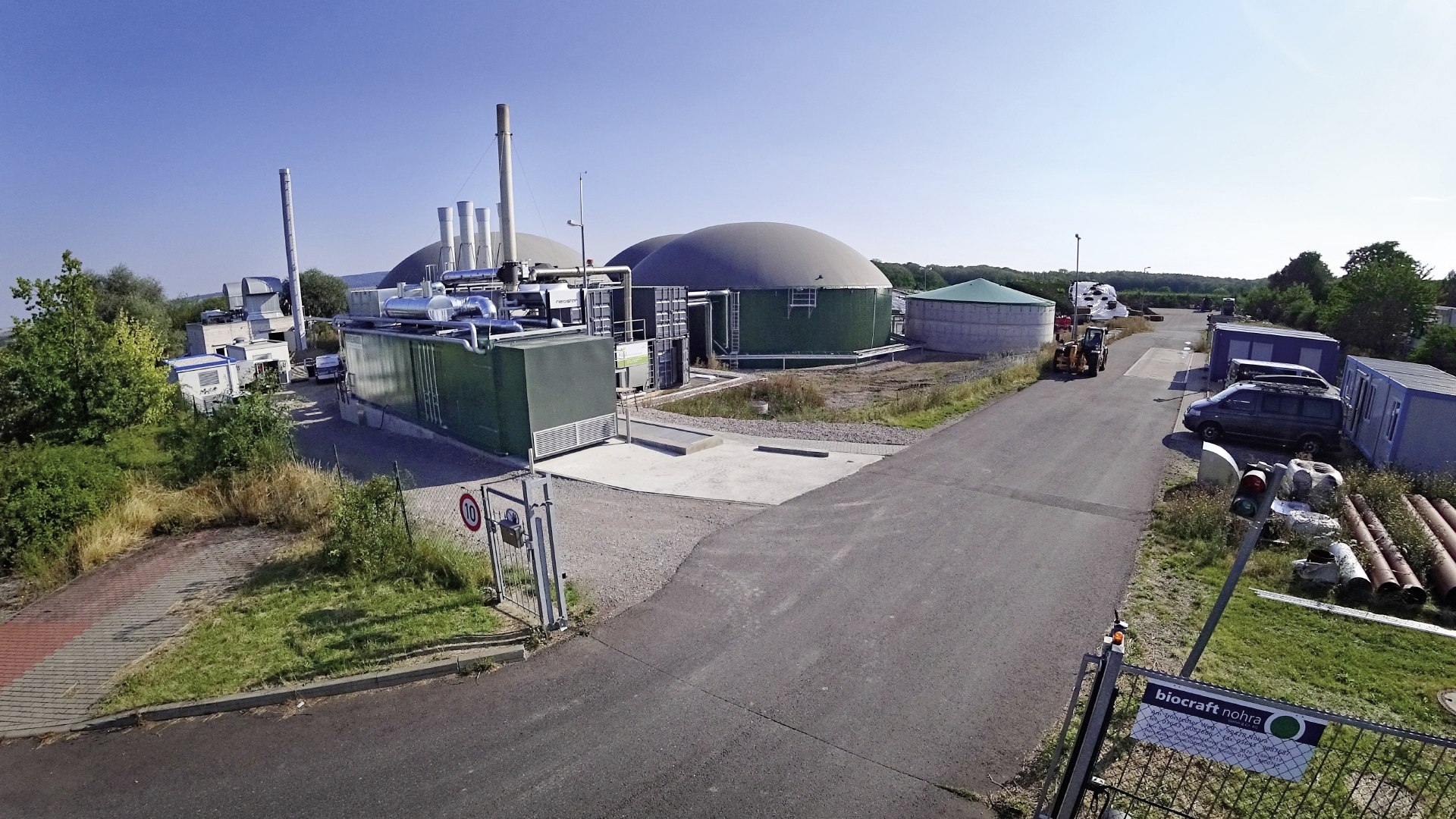
Partnership for plant optimization: In Nohra, Vogelsang and Biocraft Nohra are working with partners from industry and research on the “FlexPump” project – a mixing concept for the flexible, efficiency-optimized and multifeedstock- capable operation of biogas plants.
Successfully marketing worthless items. Colloquially in German, one also likes to say: “Making money from sh**.” In Grammetal, they take this literally – and quite successfully, actually. There, animal excrement is
economically converted into energy in the biogas plant of Biocraft Nohra. The trigger for the change in the operating concept was rather unpleasant: the neighboring industrial company, which used the entire heat of the plant, closed its doors. They had to come up with something new. Now, their efforts have been impressively successful and, in addition, added value has been created for the environment and for regional farms.
Flexpump research project with practical partner Biocraft Nohra
From the outside, the biogas plant of Biocraft Nohra looks like a very ordinary, albeit large, plant. The facility, which is located in the small district of the same name in the municipality of Grammetal, near Weimar, differs in many ways. The operators and owners are not farmers themselves, but attach great importance to close cooperation with the region’s agricultural sector. At the same time, they are open to new ideas and strive to develop the system further. It’s therefore not surprising for the plant to be a participating partner with the FlexPump research project. As part of the project, Vogelsang is working with Fraunhofer IKTS and A&U Service- und Vertriebs GmbH on a new type of mixing concept for flexible, multi-feedstock operation of biogas plants, for increased profitability. It all began in 2010 when the Plan ET plant was built as a classic 1.5 MW renewable energy plant. The digestion line consisted of a digester, a post-digester and a final storage with a respective capacity of 4,000 m³. A pusher floor with a screw conveyor system was installed for solid matter feeding.
A future-proof system
As was common at the time, the substrate mix consisted of 85 percent silage, of which 60 percent consisted of corn silage. The remaining 15 percent was dung. This mix could be supplied satisfactorily
with the dry solid matter feeding. All substrates, liquid manure, dung as well as silage came from regional farms, which in turn took back the digestate as optimized farm fertilizer. The electricity was generated in a MWM CHP unit whose waste heat was used in a neighboring slaughterhouse. This enabled additional
income to be generated. When the slaughterhouse, which until then had used all the heat, was closed, this mainstay broke and operator Andreas Kellner considered how the heat from the system could be used sensibly. Like almost all operators, he was confronted with stricter requirements and directives and the resulting costs, which forced him to increase the efficiency of the system in order to absorb the additional load. Against this background, he thought of processing fermentation residues. However, this should not only dewater the digestate. Rather, he was thinking of a solution that would make the system future-proof overall. Corn and liquid manure should be replaced by dung, increasing efficiency at the same time.
Search for the right technology
Andreas Kellner, operator of the Biocraft Nohra biogas plant (left), and Bernd Schmitz from A&U Service- und Vertriebs GmbH (right)
In his search for a suitable technology partner, he came across Bernd Schmitz from A&U Service und Vertriebs GmbH in 2018. It quickly became clear that A&U’s approaches exactly matched Andreas Kellner’s ideas. Together, they overhauled the plant concept and modified it in several places. The first conversion measures followed in 2019. Right from the start, it became clear that the new Biocraft Nohra concept is different. Instead of building an additional storage tank for digestate like most other plants, Biocraft Nohra decided to meet the new, more stringent requirements of the fertilizer regulations by upgrading the final storage to a post-digester, which created more fermentation space. The retention time was increased to 150 days. Furthermore, a new, small final storage with a capacity of only 1,000 m³ was built. No more was needed due to the new system for digestate treatment that was also set up.
New concept in the separation of digestate
First, the digestate is separated. The worth for transportation of the solid fraction obtained in this way is
increased significantly. It requires considerably fewer trips to spread it over the fields as fertilizer using a
manure spreader. Some of the liquid fraction resulting from the separation is fed back into the digester, where it reduces the viscosity of the suspension. Another part is evaporated using the waste heat and further cleaned in the process. An ammonium sulfate solution (ASL) is created, which is used as a mineral fertilizer in more distant arable regions. At the same time, around 20 m³ of water is discharged from the circuit daily. Moreover, an additional, identically constructed MWM CHP was put into operation in order to flexibly produce up to 3 MWh of electricity and, at the same time, to fully utilize the rated output of 13,000 MWh per year and to generate further income.
Instead of building additional storage room for digestate in order to meet the new requirements of the fertilizer regulations, a digestate processing system was installed.
Replacing silage with manure
Further adjustments were made to the substrate mix and the feeding technology. The plan envisaged replacing silage, and especially corn silage, with chicken, turkey and, above all, cattle dung from
regional farms. This resulted in several advantages for the system: on the one hand, a financial advantage,
because the system is remunerated on the basis of the German Renewable Energy Sources Act 2012
(EEG2012). It assigns dung to material class II, for which a fee that is 2 cents higher per kWh of electricity
is granted. On the other hand, the volume of the fed substrates or the digestate to be dispensed is reduced,
which means that overall fewer reservoir volumes and transports are required. And the new concept also
offers advantages for business partners from agriculture and the environment. Since the dung is first
fermented in the biogas plant and is no longer spread directly on the fields, methane emissions are significantly reduced. At the same time, chimeras and weeds are largely killed in the process, thus reducing the need for plant-health measures. However, analysis of the plant also showed that the viscosity of the suspension in the digester was already borderline. Reliably thorough mixing was not guaranteed. There were problems with the mixers, including a blade wing breaking. Furthermore, the solid matter feeding system was nearing the end of its technical service life. It was clear that it would not be possible to switch to dung as the main input material without making adjustments to the solid matter incorporation.
The switch from silage to chicken, turkey and, above all, cattle dung brought financial advantages, a reduction in methane emissions and fewer transports.
Chance encounter leads to successful partnership
It is thanks to a lucky coincidence that Biocraft Nohra and Vogelsang became partners in a project called FlexPump. Bernd Schmitz from A&U was sitting with employees of Fraunhofer IKTS Dresden as part of a different project when they happened to be talking about the planned project. This includes conceiving of multi-feedstock-capable operation of biogas plants for flexible biogas generation and the development of a system for hydraulic mixing in biogas plants. Necessary for the project is a suitable biogas plant that can be checked and optimized under real practical conditions and a partner from industry. Bernd Schmitz immediately thought of the Biocraft Nohra plant. It was an ideal fit for the project, especially since changes
can be identified much more quickly when using difficult input materials, such as cattle manure. And on the
technical side, too, he was convinced that a powerful liquid feeding system was required. At Vogelsang and Biocraft Nohra, the researchers found open doors. And so this exchange between experts led to both becoming partners in the project for developing and demonstrating a pump-based mixing concept for flexible, efficiency-optimized and multi-feedstock-capable operation of biogas plants.
Optimal digester mixing with installation of PreMix and DisRuptor
A pusher floor was therefore installed in Nohra as a storage bunker and a PreMix solid matter feeder was installed for bacteria-friendly mashing. The liquid
suspension is drawn off by means of a progressive cavity pump from the CC series in the lower area of the digester and mixed with the dung by the PreMix to form a homogeneous suspension. An important detail here is that heavy material such as stones and metal parts are separated out upstream of the PreMix
pump unit, moreover long-fibered components in the dung are chopped down and lumps of dung are broken up. Analyses show a significant reduction in the mean length of fibers in the suspension. This well-treated, homogeneous suspension is then pumped into the upper region of the digester.
The new liquid feeding system for solid matter incorporation consists of a pusher floor (top right) as a storage bunker and the PreMix solid matter feeder in the foreground.
Less silage. Manure content increased to 70%.
As a supplementary measure, the suspension is additionally processed by means of mechanical disintegration. For this, the DisRuptor was installed in the bypass parallel to the liquid feeding. The suspension is therefore also removed here, near to the ground. In the narrow gaps of the functional unit, fibrous components, such as straw, are grinded and frayed and resistant structures are damaged.At the front left is the CC pump for supplying the liquid phase for mashing the solids. To the right is a combination of DisRuptor and another CC pump for processing the suspension in the bypass to the digester.
The effect of mechanical disintegration can be clearly seen on microscopic images. Formerly smooth surfaces resemble a high mountain landscape, traversed by ravines and craters. The suspension prepared in this way is then also led back into the upper region of the digester, where the fermenting bacteria benefit from the enlarged surface and easier access to the nutrients. As a side effect, both measures reduce the viscosity of the suspension, and this is clearly noticeable.Microscopic images of the solids before and after treatment with the DisRuptor show the effect of mechanical disintegration.
Since the start-up of the PreMix liquid feeding and the mechanical disintegration with the DisRuptor, the dung content has increased from 15 to 70 percent. As a logical consequence of the increased dung content and the reduced supply of liquid manure and corn silage, the dry matter content in the digester rose from May 2019 to June 2020 by over 2 percent to 14.3 percent, although the centrifugate from the separation is partly returned. In the literature, such a suspension is often referred to as no longer pumpable. In Nohra, the viscosity fell continuously from 17.95 Pa s to 3.3 Pa s over the same period (measured at a shear rate of 10 s-1).
Field test
Further investigations and analyses as part of the project confirm the initial results. Simulations show significantly better mixing of the digester. At the same time, the power consumption of the mixers fell. No wonder that those involved are eagerly awaiting further results.
But the practical testing is still in the optimization phase. Andreas Kellner, Biocraft Nohra, is already satisfied with the initial results. But he hasn’t reached the end of the proverbial flagpole, either. The aim is to further increase the dung content. In addition, together with his partner Bernd Schmitz from A&U, he already has further plans for straw to replace parts of the current feed ration in the near future.
One thing is clear to both: Without the Vogelsang technology for processing the substrates or organic suspension, even what has been achieved so far would be unthinkable.
FlexPump - Development and demonstration of a pump-based mixing concept
for the flexible, efficiency-optimized and multifeedstock-capable operation of biogas plants
The further expansion of the renewable electricity system requires economical, optimized and flexible operation of existing and new biogas plants. Taking into account the given advantages such as reliability,
controllability and the wide range of possible applications, efficient concepts and technologies must be developed that guarantee sustainable, profitable operation in the long term, regardless of government
funding. There is immense potential here in optimizing the mixing of the suspension in the digester, combined with an efficient and targeted technology for substrate incorporation and pretreatment. As part of the joint project, an overall system for the hydraulic mixing of biogas reactors is being developed and tested and optimized under practical conditions on a pilot scale. Each project partner takes on a specific area of responsibility. Fraunhofer IKTS develops a process concept and evaluates the mixing process using process tomography and numerical flow simulation. The adaptation and optimization of the pump system and its process parameters are carried out by Vogelsang. In addition, a concept for regulating the overall process is being developed. A&U is responsible for the integration of the pump-based mixing system in the Nohra biogas plant, including the evaluation of the mixing system under practical conditions.
The combined know-how of various partners flows into the government-funded FlexPump project.
Related links:
Everything about the Biogas segment
More about Vogelsang CC-Series pumps
More about the Vogelsang DisRuptor