From waste to value
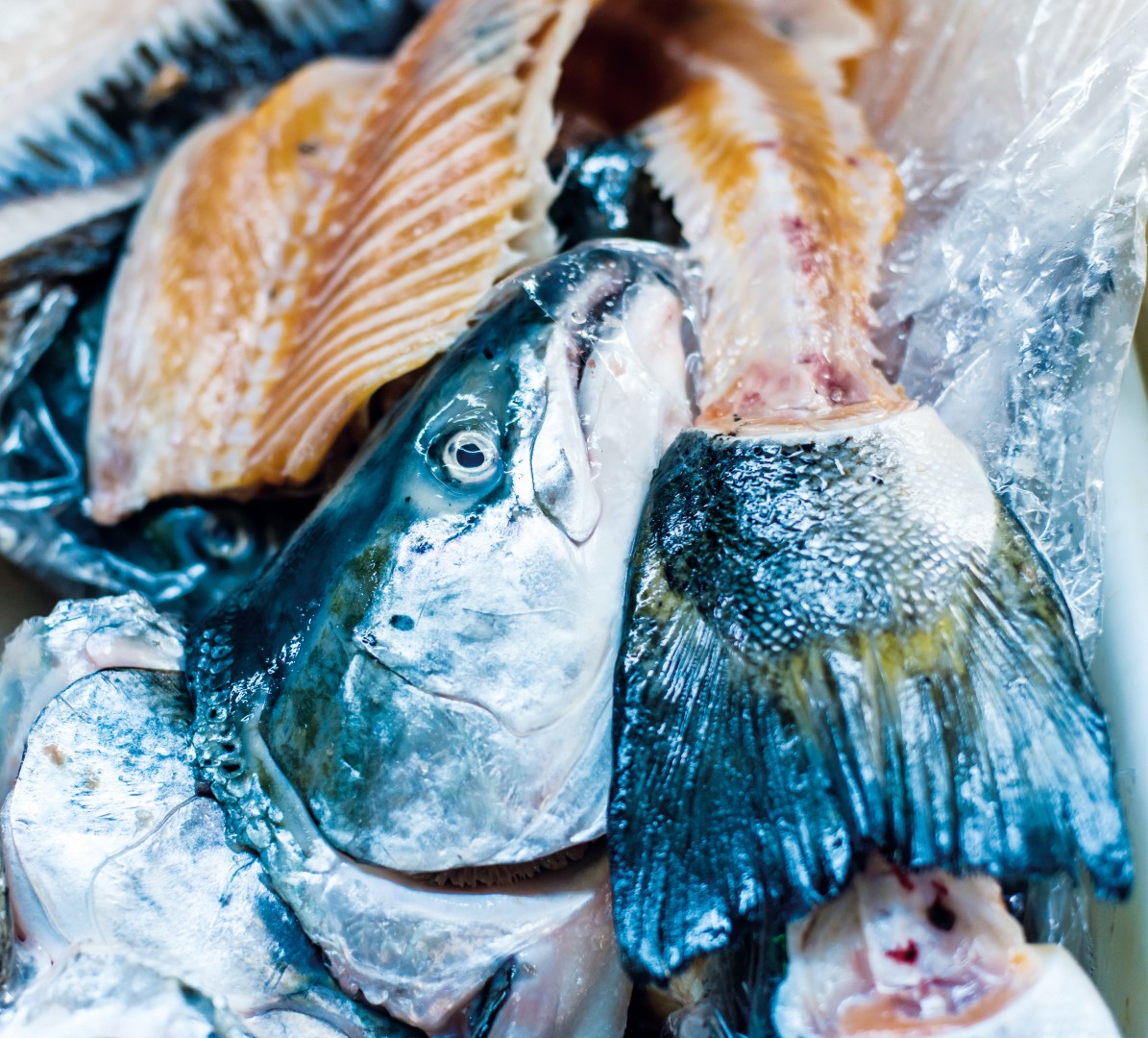
The RedUnit transforms tough food waste and by-products into pumpable media for further processing
The RedUnit is an all-in-one unit with many advantages: a modular setup for a tailor-made customised solution, lower electricity and water consumption, sturdy shredding due to the solid design of the RedUnit and extra-simple commissioning via an intelligent control system and plug-and-play solution.
Meat, bones and hooves: The 2 in1 RedUnit system will get to the bottom of abattoir waste
Markus Liebich, Industry Sales Manager Germany
“During the slaughter of animal livestock, a great deal of waste and by-products like bones, skin and offal are created. These remains provide genuine added value if prepared accordingly – for example in the manufacture of gelatin, animal feed or fertilisers. To reenter the cycle, these tough materials need to be processed into the smallest possible particles or to a pumpable suspension using appropriate technology. To do this abattoirs, gelatin manufacturers and butchers require sturdy and reliable shredders and pump systems,” explains Markus Liebich, Industry Sales Manager for Germany.
Meat manufacturing and meat products are among the largest sectors in the Irish food processing industry. 2023 Meat and Livestock sector exports recorded a value of around €4.2 billion.1 During this process, as well as the primary product, a multitude of animal by-products and waste are created that are unsuitable for human consumption or only under certain conditions. By the thorough shredding of solid matter, these can be recycled to a great extent, however.
Among other things, they can then be used for the manufacture of gelatin, animal meal, pet food or as a feedstock for biogas plants. In addition, fat and protein can be melted down from the assorted bones and abattoir waste and used as raw products for the manufacture of cosmetics, medicine or animal feed. Precise shredding into the smallest possible parts is key here. The smaller the particles, the better they can be used in subsequent processes. A prerequisite for the processing of tenacious solid matter in every case is tough, high availability, coordinated shredding and pump technology.
Sophisticated combination of pump and shredding technology
Bones, hooves, horns, feathers or offal contained in remnants place huge demands on shredders and pumps. At the same time, specific size-reduction ratios that comply with a maximum size are often required to keep using the materials accordingly. The correct preparation chain for the recycling of abattoir waste and by-products varies according to the characteristics of the solid matter to be shredded and the desired output.
With the compact RedUnit, Vogelsang has developed a practical plug-and-play solution. A combination of pump and shredding technology designed especially for the food processing and recycling industry, it offers significant benefits compared to stand-alone solutions: it requires less space and power, is simpler to control and maintain, and therefore offers maximum operational safety. Furthermore, rotors and cutting screens can be flexibly adapted to customer requirements.
Method of operation of RedUnit
RedUnit XRipper XRL – for rough grinding, a CC series progressive cavity pump – for efficient pumping, and an extra RotaCut RCQ – for fine grinding and foreign matter separation
The user specifies the solid matter and size-reduction ratio – from extremely solid to pulp. Shredders and pumps are installed in the RedUnit as modules in line with these requirements.
- Solid matter like meat remnants or bones is conducted via a hopper to the RedUnit.
- (Optional) The user adds any additional fluid required via a VX or IQ series rotary lobe pump.
The XRipper XRL coarsely shreds the raw particles to a pumpable size.
- (Optional) Finally, the CC series progressive cavity pump pumps the mixture to the destination defined by the customer, such as into a container or transfer trailer.
(Optional) The shredded medium falls into the mixing area of the RotaCut RCQ macerator to be shredded as defined. Here it is mixed with fluid. The shredding unit comprising RotaCut RCQ blade rotor and screen cut the mixture to a defined size.
RedUnit: Lots of combinations for tailor-made solutions
RedUnit XRipper XRL
The basic variant integrates the XRipper XRL shredder, which contains the required control technology for efficient optimisation of the entire unit. This solution is ideal for the shredding of large quantities of bulky materials and solid matter such as abattoir waste, potatoes, sugar beets and frozen vegetables.
RedUnit XRL + CC series progressive cavity pump
The RedUnit reduces the particle size of coarse matter in a single shredding step and mixes the medium with fluid where required to prepare it for downstream processes. The medium is pumped through the drain line with a CC series pump.
RedUnit XRL + CC series progressive cavity pump + downstream RotaCut RCQ
For special application areas such as the processing of abattoir and fish waste, a RotaCut macerator can be placed downstream of the RedUnit XRL and the CC series. This variant will provide a uniform particle size with maximum flexibility and sufficient throughput rates.
RedUnit XRL + RotaCut RCX + CC series progressive cavity pump
This combination is the most compact RedUnit solution. Offering two shredding stages on one pump stage, it is ideal for highly liquid media requiring a small particle size such as potato remnants.
Effective shredding without downtime
From poultry and pig slaughterhouses to gelatin manufacturers, companies with the widest variety of meat and processing requirements rely on the RedUnit by Vogelsang. In 2018, for instance, a poultry processing plant from the UK opted to use a combination plant consisting of the XRL shredder and a CC series progressive cavity pump by Vogelsang. In the plant, hens are slaughtered and the meat is prepared
for the retail sector. Hens that are damaged during processing or fall to the ground are removed from the line. With a weekly plant throughput of up to two million whole hens, a great deal of waste is created, around a ton of waste per hour, which needs to be processed for the pet food market.
The RedUnit enables the company to successfully handle the ongoing shredding and conveyance of these poultry remains. The RedUnit processes the remains at a speed that is adapted to the substances, enabling the pump to run at a constant speed. The shredder tools on the RedUnit are made of a block of special steel. Thanks to its single-piece design, the torque can be transferred uniformly to the rotors across the entire length of the shaft, the shredder withstands higher loads and enables the processing of up to 80 hens in just one-and-a-half minutes.
Economical and easy to maintain
The UK poultry slaughterhouse plant saves space, energy and time when compared to the shredders they used previously, as the RedUnit requires no additional downstream pumps or screw conveyors. The individual elements are stacked vertically on top of one another so that the shredded material falls directly into the integrated pump. Having no intermediate conveyance sections means that electricity consumption also drops overall. Since the RedUnit needs no water during the shredding process either, water consumption is also significantly less.
The RedUnit boasts the QuickService concept for progressive cavity pumps for fast and easy maintenance, which offers several options for the replacement of the rotor and stator and for sealing changes. If the pump needs to be operational again as quickly as possible, the stator and rotor are replaced as a single unit. The entire rotating unit can also be replaced without dismounting parts of the pipe on either the suction or discharge sides. Alternatively, the stator can also be removed and replaced or the rotor replaced individually.
A control system can be optionally added to any RedUnit combination for maximum performance.
Ready for Industry 4.0
The integrated control of the RedUnit is equipped with the platform-independent OPC UA communication model and therefore prepared for the future like smart factories. Using an intelligent control unit and an intuitive touchscreen, the user can view all technical characteristics of the individual machines and adjust these, too. The widest variety of user requirements – such as for delivery rate and shredding stages – can be adapted in the briefest of times.
The RedUnit also offers a plug-and-play solution for all combinations, making commissioning incredibly simple. In addition, the unit is commissioned by trained, qualified personnel before leaving the factory. This ensures that the system is checked professionally for operational functionality and keeps the time required for installation at the customer to a minimum. Following delivery, the RedUnit can be commissioned immediately as a turnkey solution without any additional work.
What happens with the abattoir waste during meat production?
Edible = fit for human consumption
This includes bones, skin and connective tissue. If these are classified as edible, they can continue to be used as food. One example here is the manufacture of gelatin.
Products classified as unwholesome can continue to be used provided certain regulations are observed. Fat and protein from bones are used as raw materials in animal feed, cosmetics and medicines for example.
Inedible = animal by-product
Category 1: Animal by-products with a high risk (e.g., animals with certain illnesses such as TSE) have to be burned as waste or brought to special waste sites for disposal.
Category 2: By-products that carry the risk of other illnesses, among other things. These may be used for the generation of biogas, for composting or for the manufacture of organic fertilisers after they have been treated accordingly, but not for the manufacture of animal feed.
Category 3: Animal by-products that pose no danger to the health of human beings and animals
(e.g., carcass parts such as skin, hooves, horns and feathers). These may be used as a raw material by pet food companies or processed in a biogas or composting plant.
Fat and protein from bones are unsed as raw materials in animal feed.
1) Source: Board Bia Irish Food Board, Export Performance and Prospects 2023/24 report
Further links
Discover our virtual showrooms