Pump power to go
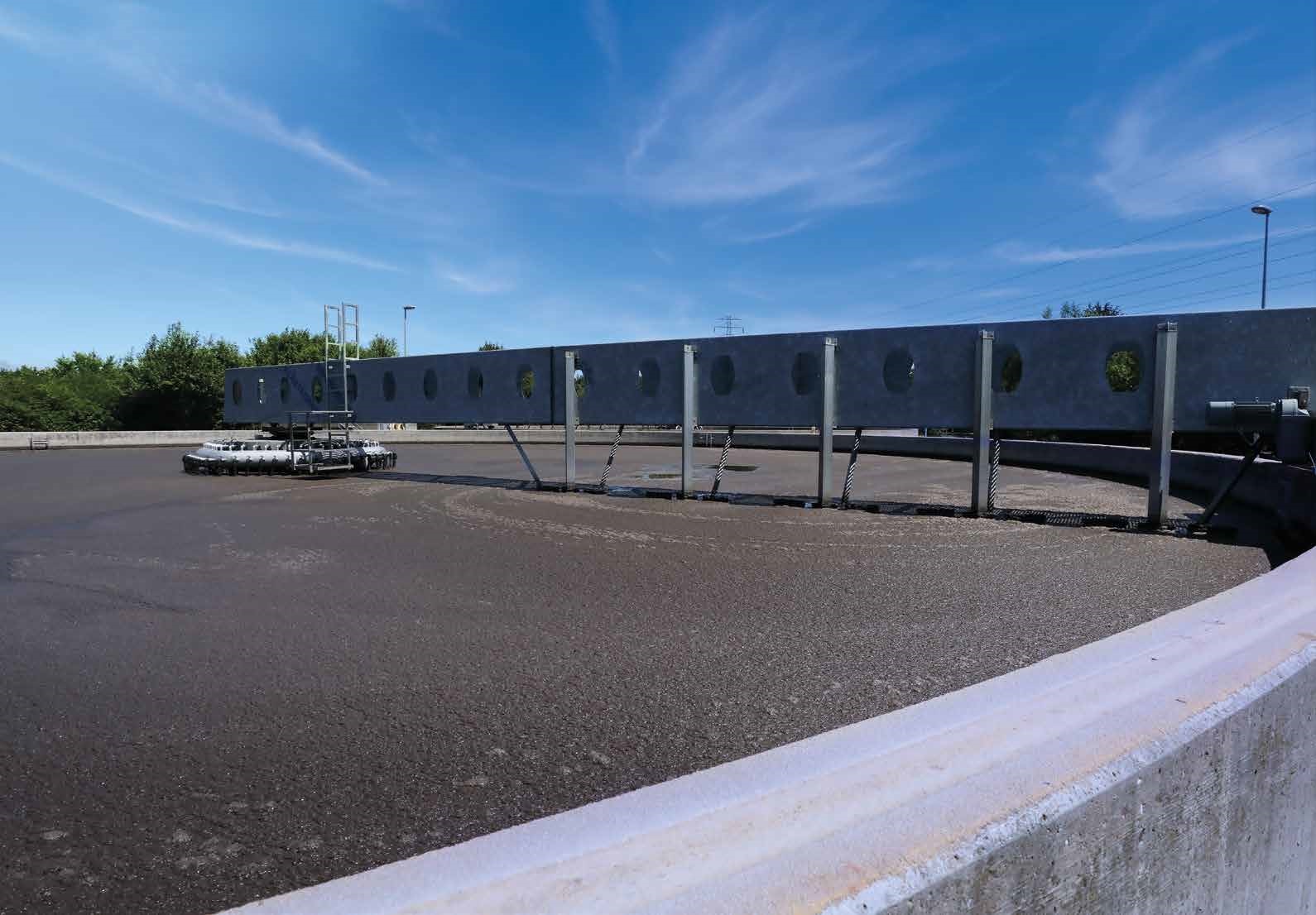
Wildeshausen wastewater treatment plant: Unconventional but simply practical. Emptying the tank with a tractor and Vogelsang pumps
Wildeshausen: The county seat in the district of Oldenburg is located directly on the Hunte river in a region rich in agricultural land and forests. The next big city is not far away and yet – or precisely because of the location – the number of inhabitants is steadily increasing. This continuous growth and the constantly increasing requirements for wastewater treatment make it necessary to continuously develop the wastewater treatment plant, which is operated by the city.
Easy tank drainage: the top priority
However, the master wastewater technician in charge, Matthias Schnieder, and his team are happy to face this task. The residents are pleased, as the fees for the predominantly domestic and commercial wastewater have been kept very stable over the past 25 years or have tended to be reduced. The secret behind this is very simple: most of the money saved through infrastructure investments is reinvested. And that pays off for the residents in the long term. One of these investments is the modernization of the biological treatment stage, in which phosphorus and nitrogen are removed from the wastewater. The necessary processes are supported and controlled by the addition of lime slurry. The sludge is also alternately exposed to anaerobic and aerobic conditions (i.e.,with and without oxygen).
Matthias Schnieder, master wastewater technician at the Wildeshausen wastewater treatment plant.
Modernization of the biological treatment stage
The nitrogen is eliminated in two stages. The nitrogen in the wastewater, which is mainly present in the form of ammonium nitrogen, is converted into nitrate by the microorganisms present in the activated sludge. In the nitrification process, the micro-organisms require a significant amount of oxygen, which is carried into the sludge by means of aeration.
During the subsequent denitrification, the oxygen is removed from the nitrate by other micro-organisms. What remains is nitrogen, part of which is released into the atmosphere as a gas while part is absorbed by the microorganisms, and thus removed from the wastewater. Anaerobic conditions are required for this process step, which is why the addition of oxygen by means of ventilation has a negative effect.
In practice, therefore, the introduction of atmospheric oxygen is repeatedly interrupted by pauses in order to enable anaerobic denitrification.
Refurbishment and modernization of the areation system, beginning in 2019
The aeration system of the Wildeshausen wastewater treatment plant, where precisely these processes take place, was expanded in 1993. As was often done at the time, two new aeration basins with interval ventilation were built and operated in parallel. The task of upgrading this part of the wastewater treatment
plant was taken up in 2019. The first step saw the installation of new turbo compressors to generate the
required compressed air; the units installed featured reduced power consumption of approx. 7.5 kilowatts
compared to the previous equipment. Moreover, since the compressors that aerate the sludge account for much of the energy consumption of a wastewater treatment plant, even small improvements translate into a considerable reduction in costs.
Moreover, the first aeration tank was renovated and equipped with new tube aerators. Next, the bustling team around master wastewater technician Schnieder used the opportunity to optimize this part of the cleaning process. Instead of continuing to operate the two tanks in parallel and switching off the ventilation repeatedly in order to create the conditions for denitrification, both process steps will now take place in physically separate areas in order to achieve superior decomposition of the organic loads.
1,500 m³ of sludge pumped from one basin to the other in just two and a half hours
The wastewater that was previously pre-cleaned in the mechanical cleaning process is now mixed with
activated sludge in the first tank , but no longer aerated. The expert speaks of an upstream denitrification
process in which the nitrate contained in the activated sludge-wastewater mixture is eliminated. At the same time, the activated sludge-wastewater mixture flows from this basin via a 600 mm pipe system in free fall into the second tank, in which the mixture is aerated efficiently and in an energy-saving manner using the ventilation technology newly installed in 2019. Under these conditions, nitrification, i.e., the conversion
nitrogen into nitrate by microorganisms, takes place in the second tank.
The nitrate-containing mixture is then pumped back into the first tank by two highly efficient propeller pumps at a flow rate of 500m3/h (per pump) via two connecting lines newly built between the two tanks as
part of the renovation project. Thanks to the optimal conditions in the first tank , as described above, the nitrate is removed from the mixture during the denitrification process.
Process engineering
By August 2020, the time had come. The decision was made to adapt the biological treatment system to the new process principle. To do this, several more installations had to be made on the recirculation lines between nitrification and denitrification, which made it necessary to reduce the level in the basins and the connecting lines to such an extent that they went dry, at least in the upper area.
Conventionally, this would have meant installing one or two large submersible pumps. An electrician would have had to temporarily lay a cable from the nearest suitable connection point and connect the pump, which a specially ordered crane truck would have to lift into the basin and then lift out again at the end.
The sludge was pumped over by two standard pumps with PTO shaftdrive mounted on a three-point base, driven by a tractor.
The Wildeshausen staff found a somewhat simpler and less complicated way to do this, in which they made use of the rural character of their region. They rented a powerful tractor with front and rear PTO (Power Take-Off) from the local agricultural machinery dealer. They rented two standard pumps with PTO drive mounted on a three-point base from Vogelsang. The equipment was set up between the two tanks. Using two standard hoses, the sludge was sucked out of the tank and pumped into the other tank. The delivery rate of the pumps could be individually adjusted using the tractor’s idling gas.
Although the sludge had to be sucked in from a depth of several meters at the end, the job was done in two and a half hours. 1,500 m3 of sludge had been pumped from one tank to the other. And at a cost that would have been incurred by the crane truck alone.
Overall, the effort put in by Schnieder and his team was worth it. The engineering processes are now running even more smoothly. The biology more robustly resists fluctuations, making it easier to adhere to the limit values during the process. And when processes run smoothly without the need for major control interventions, the result is always lower operating costs.
Further links
All about the wastewater segment
Visit our virtual wastewater showroom