Vogelsang's twin-shaft grinder at the Koblenz sewage treatment plant
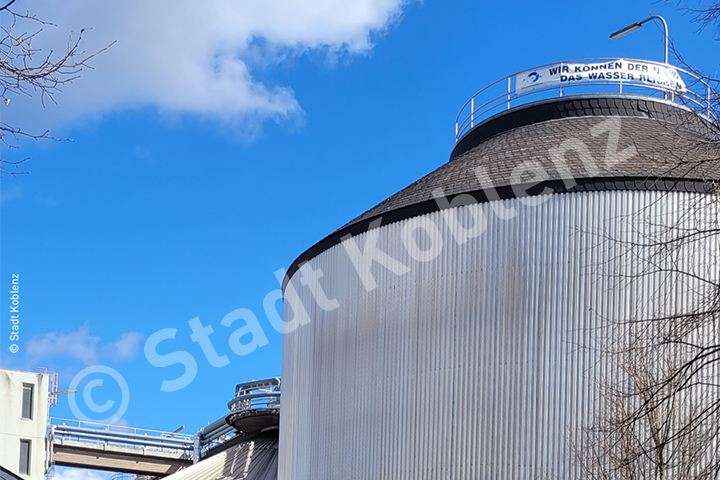
The Koblenz sewage treatment plant has been situated right on the Rhine for over 50 years. Going back only a few years, digestion tower circulation was frequently disrupted due to clogged pumps. As a solution to this problem, the sewage treatment plant now relies on the XRipper XRP
wastewater grinder from Vogelsang.
The historic city of Koblenz is located in southwestern Germany and, with its terraced vineyards and castle ruins, is considered the gateway to the Upper Middle Rhine Valley. This is where the Rhine and Moselle rivers meet. The “Stadtentwässerung” is a wastewater treatment company owned by the city of Koblenz. Among other things, the local authority operates the Koblenz sewage treatment plant situated right on the Rhine. The sewage treatment plant was put into operation in 1971 with mechanical and biological treatment for a capacity covering a population equivalent (p.e.) of 160,000. Between 1987 and 1992, the plant was expanded to 320,000 p.e. and adapted to the new requirements of wastewater technology, without any interruptions to the sewage treatment plant’s operations. Up to 30 million cubic meters of wastewater per year can be treated in this larger plant.
A lot of work for the digestion towers
The Koblenz sewage treatment plant operates two small digestion towers, each with a capacity of 2,800 cubic meters, and a large digestion tower with a capacity of 3,700 cubic meters. The digestion towers
are fed a mixture of raw and excess sludge as well as sludge from the production of beer
and local specialties at a local brewery. This sludge is rich in energy and ensures a high gas yield during
anaerobic fermentation in the digestion towers.
In the first step, all the sludge at the Koblenz sewage treatment plant is directed to the largest digestion
tower because it has the greatest buffer potential due to its high capacity. Should problematic components
such as toxins or inhibitors ever be present in the sludge, the bacteria are best able to cushion their
effects in the large-volume digestion tower. After the sludge has flowed through the first digestion tower,
it then enters the two smaller digestion towers in equal proportions. In total, the sludge remains in the digestion towers for about 28 days.
The large digestion tower (on the left) has a capacity of 3,700 cubic meters.
Problems with digestion tower circulation
Two dry-pit centrifugal pumps provide circulation and heating in the digestion tower and thus ensure
optimum decomposition of the organic matter as well as a high gas yield. Over time, clogging from foreign
material in the sludge was causing problems with circulation. In particular, the check valves of the pumps
were proving to be a critical point, as the entangled material kept on causing malfunctions. Even switching
to a different type of check valve did not improve the situation. The sewage treatment plant’s employees
sometimes had to intervene on a daily basis to clear the blockages.
Wastewater manager Ulrich Marquart and his team weighed up possible solutions and ultimately
decided to install a grinder. The experts needed a machine to reliably shred the entangled material, while also offering effortless integration into the existing system.
XRipper XRP to the rescue
Marquart and his team finally opted for the XRipper XRP from Vogelsang in a special design. Instead of
using a motor arranged above the machine, motors with bevel gears are in action at the Koblenz sewage
treatment plant. This special design was made necessary by the particular on-site conditions, as the
discharge pipe runs right above the grinder, so there was not enough space for the classic geared
motor design.
.jpg?width=660&height=440&name=%C2%A9%20Stadt%20Koblenz%20(1).jpg)
Thanks to the drive system using a bevel-gear motor, the XRipper XRP could be easily installed below the pressure line.
The XRipper XRP with bevel-geared motor was easy to install in the confined space, while still ensuring
sufficient room and good access for service and maintenance work. A year after the first Vogelsang
grinder had been put into operation, the team at the sewage treatment plant decided to install another
XRipper upstream of the second centrifugal pump.
Trouble-free pumps
Today, maintenance interventions are rarely required for rectifying malfunctions caused by entangled material. The XRippers do a great job, reliably shredding the entangled fibrous solid matter and thus preventing clogging of the pumps. The digesters are optimally ciculated again. Only a few stones need to be removed from the stone catcher every one to two months. The employees haven’t yet been able to determine where the stones are coming from. But it is better to eliminate them than for them to show up elsewhere in the process at some point.
Reliable digestion tower circulation: thanks to the two upstream XRippers, less service and maintenance are required for the two circulation pumps.
The Koblenz sewage treatment plant has since additionally installed two Vogelsang RotaCut RCQ macerators in the sludge dewatering system. They are located upstream of the dewatering centrifuges
and ensure the smooth operation of the sludge dewatering system.
Degestion towers briefly explained
The egg-shaped digestion towers are often found in larger sewage treatment plants. They contain the sludge that is produced when cleaning wastewater in a sewage treatment plant. Mixers and pumps constantly circulate the sludge in the absence of air at temperatures of about 36°C. The digestion towers ensure that the organic components of the digested sludge are broken down by bacteria in a controlled manner under oxygen-free (anaerobic) conditions.
Among other things, digester gases with a high methane content are formed. These are captured because of their strong greenhouse potential and utilized for energy, for example, to generate heat in a boiler or electrical and thermal energy in a combined heat and power plant. The energy generated in this way is mostly used directly in the sewage treatment plant, reducing the cost of purchasing electricity and gas from outside sources. In addition, the energy can be sold to third parties.
Related links: